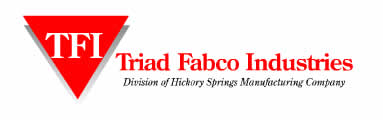
Parts listing by the 1st digit and their meaning:
100 series STANDARD DOT BACKS Back Height 25" to 27"
200 series N.Y. DOT BACKS Back Height 29" to 31"
300 series STANDARD REAR BACKS Back Height 25" to 27"
400 series N.Y. REAR BACKS Back Height 29" to 31"
500 series STANDARD PRE DOT BACK
600 series N.Y. PRE DOT BACKS
800 series BARRIER BACKS
900 series SEAT CUSHIONS
Note: Last two digits of part specifies size; Letter preceding part
number is style of bus (example: C139 is a Carpenter 39" DOT Back)
The following listing is for the styles that have backs other than the standard listing
WARD DOT BACKS
WD-1390 1977-86
WD-139 1986-94
WD139-94 1994-UP
WAYNE DOT BACKS
WY-139 1977-90
WY-139-91 1993-UP
Note: Wayne and Ward 1390 are the same back.
Freight
A. Capable of shipping small package, or truckload.
B. Allows customers to use TFI freight discounts.
C. Pass freight savings to customers.
Environmental
A. Triad Fabco recycles pre-consumer virgin foam scrap.
B. Triad Fabco has an environmental policy in place for disposing of all hazardous materials.
Molded Rebond buns
A. Density ranges from as little as 3.5# up to 9.0#
B. Bun thickness ranges from 8” to 16” depending on density
C. 2 standard bun sizes 43 X 91, and 55 X 78.
D. Able to meet either FMVSS302, or C117.
Golf Cart/Electric Car Cushioning
A. Triad Fabco is the largest supplier of rebonded molded cushioning in the US.
B. OEM golf cart supplier for over 30 years.
C. Molding golf cart cushions allow for a higher density product at a lower cost.
D. Molded rebond foams provide excellent comfort without sacrificing serviceability.
E. Our products are designed to perform in the golfing environment.
This includes the freezing temperatures of Canada, to the hot humidity of southern Florida.
F. Our molding process allows us to vary the density throughout the cushion.
This allows us to firm up the corners for a better upholster fit, while offering a softer center for a more comfortable ride.
G. The higher density of the molded rebond foams reduce the possibility of foam softening.
Which means a longer tailored upholster look. When testing the Support Modulus and Height Retention (Sag Factor) of our molded foams we consistently outperform virgin foams.
H. Triad Fabco has the ability to offer molded cushioning and back pads in various shapes and sizes for customers that require a unique look.
I. Triad Fabco has the ability to custom fabricate for those low volume custom needs.
J. Our rebonded foam meets FMVSS 302.
School Bus Seating
A. Triad Fabco Ind. is the largest supplier of molded rebonded foam to the industry.
B. All parts constructed to meet where applicable FMVSS 222, and FMVSS 302.
C. Because rebonds have a higher density than virgin foams they do not soften or breakdown as quick as virgin foams.
D. Our molding process allows us to vary the density throughout the cushion. This allows us to firm up the corners for a better upholster fit, while offering a softer center for a more comfortable ride.
E. The higher density of the molded rebond foams reduces the possibility of the foam softening over the frame. Each time virgin foam is compressed their cell walls weaken. The weakening of the cell walls causes softening of the foam (loss of compression). How quickly the foam softens is determined by the density of the foam. Since virgin foams are a lighter density than rebonds they tend to soften very quickly. Virgin foam density can range from 1.0 to 2.0 pounds per cubic foot, while molded rebonds are minimal of 3.5 up to 12.0 pounds per cubic foot.
F. TFI’s molding process provides greater consistency that cut/fabricated foams. Molded foams offers consistent outside dimensions, radius, and density. Virgin foams are cut on either a bandsaw or a contour cutter. Every dimension can vary based on the consistency of the equipment.
G. Molding reduces the number of glue seams, thus reducing the potential for failure. Our molded back pads only have one major glue seam. This seam is reinforced with a heavy nonwoven material. This material protects the back pad from the friction of the frame against the foam seam.
H. We test for premature breakdown or our Flex Fatigue Tester. This machine simulates the stress the foam back pads go through when a child pulls on the back pad as they exit the bus. We stress the corners and center head area of the back pad 3-1/2”. We currently exceed 250,000 cycles without foam failures.
I. Triad Fabco is willing to invest in technology to improve the quality of its product. We have automated the adhesive spraying of our assembly line. This allows us to guarantee the proper amount of adhesive will be placed on each back pad.
J. Triad Fabco has developed a high temperature sear resistant adhesive. This reduces the likely hood that the glue seams will open up on those hot days in the desert of Arizona, or become brittle in the frozen north.
K. Rebond foam meets FMVSS standards and is currently being used in the majority OEM back pads.
|